産業技術総合研究所(産総研)のエネルギープロセス研究部門(つくば市小野川、望月剛久研究グループ長)は6日、二酸化炭素と水を原料に、液体合成燃料を一貫製造する原型的なプラント装置を開発し、連続運転に成功したと発表した。
設計データを測定するためのベンチプラントと呼ばれる施設で、パイロットプラントの前段階となる。同研究部門がカーボンニュートラル燃料技術センター(JPEC、東京都江東区)と共同で産総研つくば西事業所内に約1000平方メートル規模で整備した。2020年度から5年をかけての事業で、連続運転により今回、1時間当たり200ミリリットルの液体合成燃料が製造できた。
液体合成燃料はガソリン、軽油、ジェット燃料など内燃機関向けの燃料を代替する。輸送や給油所などで既存のインフラを活用できるため、二酸化炭素を利用して液体合成燃料を製造することはカーボンニュートラルを実現するための有力な技術として注目されている。化石燃料を原料としない水素の製造コストが高く、どう効率化するかが大きな技術的課題となっている。
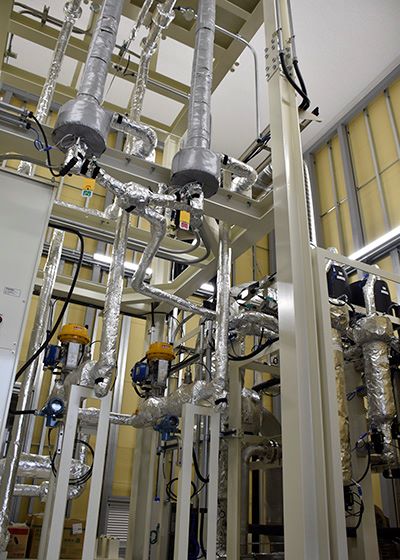
国内初
今回開発した一貫製造ベンチプラントでは、電気分解と触媒による化学合成とを組み合わせた製造プロセスを採用した。特に電気分解にSOEC(固体酸化物形電解セル)共電解を用いたシステムは国内初の設置例となった。固体酸化物形電解セルにより、二酸化炭素と水蒸気を同時に高温で電気分解させること(共電解)で、一酸化炭素と水素の混合ガスを製造可能な技術。
これまで別々に行っていた水電解による水素製造と合成ガス製造を同時に行うことで、高いエネルギー効率が期待できた。さらに触媒を用いたFT(フィッシャー・トロプシュ)合成のプロセスでは、酸触媒を組み合わせて用いることで、炭素数をコントロールしてガソリンや軽油など、液体合成燃料として利用可能な合成粗油を効率的に得られるようにした。
このプロセスにより、従来法に比べ投入電力を25%程度軽減できると試算できたことから整備に取り組み、ベンチプラントは9月から稼働開始した。
水と二酸化炭素を原料に、電解システムへ1時間当たり最大1500リットルの合成ガスを投入した。FT合成を経ての連続運転で、ガソリンや軽油成分を持った液体合成燃料は200ミリリットルが製造できた。
今後に向け、研究グループは「投入電力を多くすればその分多く生産できると思うが、化石燃料を減らし、再生可能エネルギーをどう使っていくかが課題の取り組みなので、どんな生産規模がいいのか、どんな組み合わせがいいのかなど色々データを取っていきたい」としている。(相澤冬樹)